Anomaly detection helps you stay ahead of your competitors and stay on top of the trend. You can monitor your whole manufacturing process in the industry and maintain the quality easily. You can achieve significant operational cost savings and reduce equipment downtime with mature anomaly detection capabilities. Are you interested? Some companies specialize in anomaly detection and can help you build and integrate customized camera vision systems to detect deviations in your business units.
So, what is anomaly detection? How does it work? And how can they be integrated into their functions and workflows? Let’s dive into this article to uncover all the aspects.
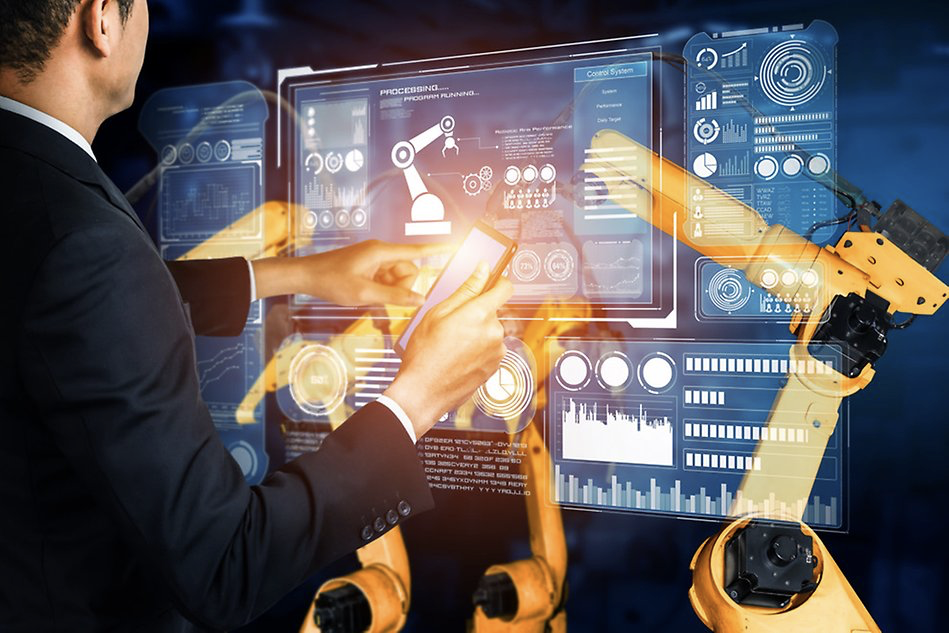
What is an Anomaly Detection?
It is a type of technique that is used to analyze visual data within a company’s operations. Anomaly detection uses visual information to identify deviations from the established baseline. This baseline represents the standard behavior of visual datasets. By doing this, the system can pinpoint anomalies such as equipment malfunctions, customer pattern alterations, or other visual domain irregularities.
What is an Anomaly?
An anomaly refers to an irregular visual element that deviates from its standard patterns. These deviations are identified through visual content analysis, such as pictures, to fix any critical issue. For example, in industrial settings, an unexpected change in machinery behavior captured through visual monitoring will be an anomaly. It may indicate potential equipment issues or deviations from standard operational values. And the engineer will fix it. It does not always indicate a critical concern, but sometimes, these visual anomalies provide the predictive investigation to address any issues early.
What are the common practices applied in anomaly detection?
Manufacturers have many different ways and approaches to detect anomalies. The three main approaches are object detection, anomaly detection, and segmentation.
Object Detection:
In this approach, the focus is on identifying and locating specific objects within visual data. Advanced algorithms are employed to recognize and highlight particular elements of interest, such as machinery, products, or components, in images or videos.
Example: Detecting and locating specific products on a manufacturing line to ensure correct assembly or identify defects.
Anomaly Detection:
Anomaly detection practice includes analyzing visual information to identify irregularities or unexpected behavior within the visual dataset. Unlike traditional data-driven anomaly detection, this approach relies on visual cues to spot deviations from established patterns.
Example: Detecting unusual machine movements or unexpected changes in the visual output of manufacturing processes.
Segmentation:
Segmentation involves dividing an image into meaningful segments or regions. This technique is valuable for identifying and isolating specific areas of interest within a visual dataset, allowing for a more detailed analysis of each segment.
Example: Segmenting medical images to highlight specific organs or anomalies for diagnostic purposes.
Applications of anomaly detection in manufacturing
Anomaly detection is one of the most important activities in the manufacturing industry, and there are many practical applications, such as scrap reduction, quality tests, compliance tests, etc. Many machine learning applications are available for anomaly detection and are doing a good enough job. In this study, we describe various applications for anomaly detection in the manufacturing fields of automobiles, tools, metals, and consumer goods, as well as some of the latest techniques available in the literature to perform anomaly detection.
Let’s look at ways in which computer vision and Industry 4.0 technology can enable robust anomaly detection.
1. Product Quality Control
Before packaging and shipping a product, manufacturers must ensure that each item meets the required product standards. However, manual visual inspection is tedious, even for experienced quality inspectors.
In addition, microscopic examination of small product parts takes significantly longer than done manually or automatically. Complex components, such as circuit boards, are made from multiple components that must be assembled in a specific way for the final product to work. With automated computer visual inspection solutions, product defects can be placed more easily and quickly. Manufacturing quality control also extends to the packaging and labels used for each product and the products. Failure to identify defects early in the process, such as incorrect labeling or package damage, can result in delayed customer shipments, returns, or complains
2. Productivity and Efficiency
Manufacturing is an inherently complex process that requires continuous monitoring of many steps to minimize production delays and product quality issues.
These steps usually include the following:
- Bringing raw materials into manufacturing facilities
- Production of product parts at these facilities
- Assemble these parts into final products
- Inspection to Assess Product Quality
- Package of inspected product for ready for shipment
- Ship Product to Customer
Computer vision anomaly detection allows picture analyses from each process to be collected in real-time, so if a problem occurs, it can be addressed without further delay.
Using Anomaly detection guides to detect abnormalities is also useful for evaluating the productivity of an assembly line or the entire production line. Multiple people, processes, and tools are involved in manufacturing, making it difficult to track productivity-related issues.
Detecting defects in the manufacturing process
Visual inspection helps companies in different industries look at the quality of the product and its condition. Image processing can monitor manufacturing processes such as cleaners, film deposition, etching, damage, injection, resist coating, and heat damage. This model can detect wafer-level abnormalities and automate processes such as pre-placement inspection.
The rules are the same, and a visual inspection system developed on a deep learning algorithm learns to be trained on good-quality images to detect defects efficiently.
Predictive maintenance
Downtime of manufacturing equipment is becoming more costly. Predictive maintenance uses ML-based manufacturing anomaly detection to detect variations from the normal performance of the equipment long before a machine fails. Such predictive maintenance solutions integrate all relevant data from IoT sensors and smart cameras and analyze equipment health, environmental data, machine specifications, and notes by equipment operators. Insights are used to identify shifts from normal performance, predict imminent failures, and/or perform early maintenance.
Minimize Safety Hazards
To avoid such amazing statistics in manufacturing, make the most of the computer vision software. The solution uses production facility video footage and vision technologies such as object detection, vehicle monitoring, and face recognition to find employees who don’t follow safety protocols and risk their own or fellows’ health. This includes not following machine maintenance rules, not wearing protective equipment, incorrect behavior, violent behavior, etc. Affect detection is used for this purpose.
Full feedback system
This type of system allows manufacturers to develop custom-made end-to-end systems. Get a fully managed system that enables rapid development and operational processes. The system is flexible enough to support most of the standard hardware and software used on the production line. Internal teams can integrate existing hardware and software stacks into these systems. You can also use tools and services that you can use right away. These tools and services can also be customized to match the workflow of the production line.
This is a good option if you want to build a fully flexible, scalable, and optimized defect detection system to match your production line workflow. This system may be improved to better respond to changes over time. Bottlenecks related to the manufacturing line data and the computer vision’s abnormality detection model are completely transparent, traceable, and observable. As your manufacturing line requirements change, you can also select and swap anomaly detection models for different manufacturing use cases.
For Example, Anomaly detection can be employed to monitor machinery and equipment on the manufacturing floor. Anomaly detection algorithms can analyze visual data, such as live camera feeds or images, to identify irregular movements, abnormal vibrations, or unexpected changes in machine behavior. This can help detect potential malfunctions or breakdowns before they lead to production issues.
Examples of anomaly detection in manufacturing
Surface Inspection in Metal Casting:
Within the domain of metal casting, computer vision emerges as a meticulous inspector, examining surfaces for imperfections. Its discerning gaze extends to cracks, voids, and irregularities, ensuring that the resulting metal components boast both high quality and structural soundness. This technology serves as a critical guardian, guaranteeing the integrity of each cast product, from molten alloy to the final, solidified masterpiece.
Anomy detection in PCB Manufacturing:
Navigating the intricate landscape of PCB manufacturing, computer vision systems specialize in Anomy detection. Their analytical power delves into printed circuit boards to analyze layouts for any deviations. By identifying anomalies that may impact electronic device functionality, these systems play a vital role in upholding the precision and reliability of PCBs across various industries.
Composite Material Inspection:
Within industries dealing with composite materials, computer vision serves as an inspector of structural integrity. It examines composite structures for anomalies such as delamination and fiber misalignment. It safeguards the integrity of components that are crucial to aerospace, automotive, and diverse sectors, ensuring that each composite creation meets the standards of quality and reliability.
Glass Quality Control in Manufacturing:
In the glass industry, computer vision serves as a necessary inspector of glass manufacturing. This technology ensures that every glass product meets high-quality standards by examining for defects like scratches, bubbles, or impurities. Computer vision contributes to the production of glass components that are not just functional but also aesthetically superior.
Plastic Injection Molding Defect Detection:
Molten plastic takes shape within molds, so computer vision examines each product for changes. Computer vision easily detects the accuracy of short shots, warping, and inconsistent molding deviations.
The versatility of plastic injection molding makes it a basis of manufacturing in sectors ranging from healthcare to consumer goods. By detecting defects in real time, computer vision becomes an integral part of ensuring the quality of each molded product that meets the specifications.
Anomaly Detection in Welded Joints:
Computer vision is a vigilant examiner of welded joints for anomalies in the welding industry. Its sharp vision has the potential to detect issues like incomplete fusion, cracks, or misalignments. As a digital guardian, this application ensures that welded components maintain structural robustness across diverse manufacturing processes. In the crucible of molten metals, computer vision becomes a reliable partner, detecting imperfections that might skip. From seamless fusion to crack-free structures, it contributes to products that withstand the test of time and structural demands.
Rubber Quality Inspection:
Stepping into industries saturated with rubber components, computer vision helps to maintain the quality of rubber products. With precision, it inspects surfaces, identifying anomalies like air pockets, tears, or deformities. It ensures the end product meets the standard of both quality and dependability. From delicate air pockets to tears, computer vision contributes to the creation of rubber products that meet the highest reliability standards. It stands as an essential component in industries where rubber’s flexibility and durability are paramount.
CNC Machine Tool Monitoring:
In the industry of precision machining governed by CNC machines, computer vision systems take on the crucial role of monitoring tool paths. In detecting deviations in these paths, computer vision is the top technology, ensuring exact machining while identifying anomalies arising from mechanical glitches. As CNC machines carve complex designs, computer vision becomes the vigilant eye, ensuring each cut adheres to programmed specifications. Errors in mechanical malfunctions are identified in real-time, preserving the efficiency of the manufacturing process. In industries where precision is paramount, computer vision develops as an essential tool in the search for perfection.
Product Assembly Verification:
Within the orchestrated ballet of product assembly, computer vision emerges as an unwavering verifier, ensuring the correctness of each step on the production line. Beyond inspection, it guarantees components are not just assembled but properly aligned and connected. As products take shape, computer vision becomes the discerning eye verifying the accuracy of each connection. Any deviations from the intended assembly process are promptly identified, allowing immediate corrective actions. This application is a testament to computer vision’s role as a guardian of quality in manufacturing, actively ensuring that each product leaving the assembly line is a manifestation of precision and correctness.
FAQs: Applications of anomaly detection in manufacturing
How does anomaly detection in manufacturing enhance product quality?
Anomaly detection in manufacturing ensures product quality by identifying deviations from standard processes. This technology scrutinizes various parameters, from material integrity to production line behavior, ensuring that anomalies such as defects or irregularities are promptly detected. By preventing subpar products from reaching the market, manufacturers can maintain high standards and customer satisfaction.
What manufacturing processes benefit most from anomaly detection?
Anomaly detection is versatile and applicable across various manufacturing processes. It proves particularly beneficial in welding, machining, and assembly lines, where deviations such as incomplete fusion, tool wear, or misalignments can significantly impact the final product’s quality and structural integrity. The technology acts as a proactive safeguard in these intricate processes.
How does anomaly detection contribute to manufacturing?
Computer vision plays a pivotal role in visually assessing manufacturing processes. It employs advanced algorithms to analyze images or video feeds, identifying deviations from expected patterns. In welding, for instance, computer vision can detect cracks or incomplete fusion, ensuring that the structural integrity of components is not compromised during manufacturing.
Can anomaly detection prevent production disruptions in manufacturing?
Yes, anomaly detection can help prevent production disruptions by identifying issues such as tool wear or misalignments in real-time. By alerting operators to potential problems, manufacturers can schedule timely maintenance, replacement, or adjustments, minimizing downtime and providing constant product quality throughout the manufacturing cycle.
How does anomaly detection contribute to cost savings in manufacturing?
Anomaly detection contributes to cost savings in manufacturing by reducing waste and minimizing the need for rework. Early identification of defects or deviations allows for prompt corrective actions, preventing the production of faulty components. This efficiency improves overall product quality and reduces material and labor costs associated with rectifying issues later in the manufacturing process.
Is anomaly detection with computer vision only relevant for large-scale manufacturing operations?
No, anomaly detection with computer vision is relevant for manufacturing operations of all sizes. Whether in large-scale industrial facilities or smaller production setups, the technology provides valuable insights into process deviations, ensuring the quality and consistency of manufactured products. Its scalability makes it adaptable to diverse manufacturing environments.
Can anomaly detection be integrated with existing manufacturing systems?
Yes, anomaly detection systems are designed to integrate seamlessly with existing manufacturing systems. Whether it’s a CNC machine, assembly line, or quality control process, these systems can be customized to complement and enhance the capabilities of the current manufacturing infrastructure. This adaptability ensures a smooth integration without significant disruptions to ongoing operations.
Conclusion
The Anomaly detection system based on computer vision is more economical than a conventional inspection method. However, concerns about non-quality cost (CONQ) should be noted when adopting it. In short, these systems are products that have a process from development to deployment to the manufacturing line. The choice of design determines the value of the system. The anomaly detection system becomes an integral part of the manufacturing ecosystem, offering a dynamic solution to quality assurance challenges. At the same time, cost-effectiveness is a compelling advantage. The long-term success of these systems hinges on a thoughtful and meticulous approach to their development and integration into existing manufacturing processes.